One of the world’s leading manufacturers of customized pumps asked Advanced Design Technology to design a complete Turbocharger system including both pump and turbine using the 3D inverse design approach available through the TURBOdesign Suite software.
The customer set the requirements at both design and off-design conditions in terms of head and power, along with a minimum target efficiency for the complete system.
Preliminary System Design
During the initial preliminary design phase, TURBOdesign Pre was used to estimate the pump and turbine stages overall sizing and hydraulic performance; TURBOdesign Pre is a 1D sizing and preliminary design code which only requires basic duty point requirements such as head, RPM and volume flow-rate to provide the meridional shape per component and estimates of efficiency and power, the code was used to ensure matching between the two stages. The quick iterative process allowed ADT designers to quickly evaluate geometrical sizing and hydraulic performances for given design point requirements and obtain suitable preliminary stage design data. TURBOdesign Pre directly exports the meridional shape and all the required data for the detailed 3D blade design of both pump and turbine impellers into TURBOdesign1.
3D Pump Impeller Design
The meridional shape, number of blades and component specific work rVt (ie. impeller head) were loaded from TURBOdesign Pre into TURBOdesign1 for the detailed 3D design of the pump impeller. TURBOdesign1 is unique blade design software that uses the 3D inverse design approach to compute the blade shape for a given blade loading distribution.
It is well known that the main source of hydrodynamic loss in medium specific speed centrifugal pump impellers is the formation of secondary flows in the impeller, so ADT engineers started the impeller design with a spanwise loading distribution known to systematically suppress secondary flows. Such blade loading, represented in Figure 1, features an aft-loaded hub that increases surface velocities on suction surface of hub and a fore-loaded shroud that removes surface velocities on suction surface of shroud. This span wise loading distribution results in a reduction of static pressure gradients on the suction surface. Hence, suppresses secondary flows results in high impeller efficiency and the more uniform exit flow ensures very good stage efficiency.
3D Turbine Impeller Design
The turbine impeller was also designed in TURBOdesign1 following a similar process and principles as the pump impeller design, the aim being to achieve high total-to-static efficiency by reducing the accumulation of low momentum flows and exit swirl at the impeller trailing edge. To achieve this target the initial turbine impeller was designed with a fore-loaded hub and mid to aft-loaded shroud as presented in Figure 2.

A design system based on TURBOdesign1 facilitates development and transfer of design know-how across designers, projects and teams, resulting in improved engineering productivity and company’s industry competitiveness. These unique advantages 3D inverse design approach implemented within TURBOdesign1 ensures the design inputs are based on aerodynamic / hydrodynamic design parameters instead of geometrical blade angles.
Pump and Turbine Volute Design
The pump and turbine volutes also play a critical role in ensuring the system can achieve very high efficiency at design and off-design conditions within a compact packaging. Volutes are traditionally designed assuming a uniform flow coming into the volute. There is significant circumferential variation of velocities within the volute inlet particularly at off-design conditions at higher flow than the design point.
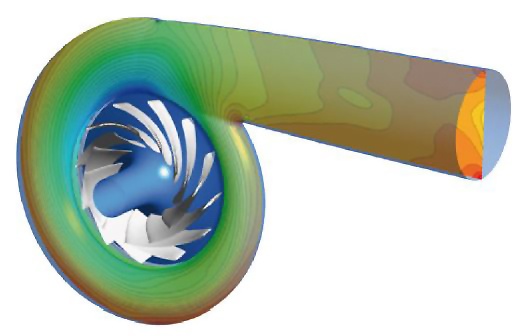
Most volute designers are well aware of this issue and tend to oversize the volute, shifting its best efficiency point at higher than the design point to counter the effect of these high losses. Using this practice the volute sizing increases and creates a mismatch between best efficiency point of the impeller and the volute, resulting in overall lower efficiency at design point.
For this project ADT engineers have used TURBOdesign Volute to design both the pump exit volute and turbine inlet volute. TURBOdesign Volute is a unique design code which allows designers to specify non-uniform circumferential flow variation at the inlet of the volute, the code then uses the streamline curvature method to calculate the outer volute flow boundary and automatically provides an optimal volute area distribution.
The final output is a clean 3D surface IGES file which is ready for meshing and 3D CFD analysis. The resulting pump and turbine stages can be seen in Figures 3 & 4.
Conclusion
During the course of this project ADT engineers have used the proprietary tools TURBOdesign Pre, TURBOdesign1 and TURBOdesign Volute to design and optimise all the components of a hydraulic turbocharger plant system for reverse osmosis desalination. The unique features provided by ADT’s TURBOdesign Suite allowed ADT engineers to explore large areas of the design space within a very short product development timeframe and ensured the best performances could be achieved by the hydraulic turbocharger system.
The full system was finally analysed with 3D CFD and the results confirmed all the Customer duty points requirements were met with a target efficiency exceeded by 5 points. You can download and the read the full consultancy summary in full: Hydrodynamic Design of a Turbocharger Pump and Turbine for Reverse Osmosis Desalination Plant Applications.
Related articles:
Share This Post