Frequent changes in the operating modes pose significant challenges in the development of a pump turbine with high efficiency and stability. In the current publication on Investigation on Flow Characteristics of Pump-Turbine Runners With Large Blade Lean in the Journal of Fluids Engineering, two pump-turbine runners, one with a large positive blade lean and the other with a large negative lean, are investigated numerically and experimentally. These two runners are designed by using the optimum stacking condition at the high-pressure edge (HPE). The experimental and numerical results show interesting outcomes on efficiency performances and pressure fluctuations. The internal flow field analyses clarify the effects of the blade lean on the pressure distribution around the runner blades. In the turbine mode at partial load, the negative blade lean can control flow separation in the high-pressure side of the runner and then reduce the pressure fluctuations in the vaneless space.
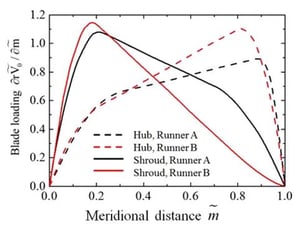
Pumped storage power stations are experiencing rapid development in China with the increasing development of the smart grid and extensive development of nuclear and wind power stations for renewable energy. As a key component of the mechanical part of pumped storage power stations, the reversible pump turbine has the function of water pumping and electricity generation as the load varies in the electricity grid. High efficiency, no cavitation, and good stability are important standards to evaluate the performance of a pump-turbine unit. Compared with efficiency and cavitation, it is difficult to evaluate hydraulic stability due to its unstable characteristics in the design stage.
Hydraulic stability in a pump-turbine has become more and more prominent with the increase of the pump-turbine’s capacity. In the pump-turbine, pressure fluctuations may arise from system instabilities generated by a combination of the pump-turbine runner’s S-shape characteristic and a hydraulic system or due to flow instabilities, such as vortex shedding, rotating stall, draft tube vortex, and so on. These pressure fluctuations can induce mechanical vibrations and even premature mechanical failures.
It has been recognized that pressure fluctuations in the space between runner blades and guide vanes are the most detrimental to hydraulic stability. The space between the runner blades and the guide vanes is usually referred to as the vaneless space. It has been shown that within the vaneless space, rotor–stator interactions (RSI) are the primary cause of the pressure fluctuations in the turbomachinery.
Many experimental and numerical studies have been made on pressure fluctuations in both model and prototype pump turbines. Near the best efficiency point (BEP) for both the turbine and pump modes, the amplitudes of pressure fluctuations are low, and the dominant frequency was blade passing frequency. At off-design conditions, amplitudes of the pressure fluctuations increased and low-frequency components occur due to the unsteady vortex formation in the runner and/or guide vanes. The alternate vortex formation leads to unsteady momentum exchange between runner blades and guide vanes and is accordingly associated with pressure fluctuations.
Many studies have been done on the RSI’s mechanism and characteristics in pump turbines. However, few investigations have been made in the design stage to reduce the pressure fluctuations and their unsteadiness. Larger vaneless space and higher height of the guide vanes can bring down the pressure fluctuations in the vaneless space.
However, these parameters inevitably affect the efficiency of the pump turbines. Leaned blades have been used extensively in turbomachinery over the last couple of decades. The main effect of the blade lean is to introduce a spanwise blade force, and then the loading distribution on the blade surface is changed. Blade lean can be used as a powerful tool to control blade loading, discharge angle, and mass flow distribution along the span. It has been noticed that the lean at the high-pressure edge (HPE) on the runner can disperse the flow impact between the guide vanes and the runner blades in the pump turbine.
In this paper, two reversible pump-turbine model runners, one with a big positive blade lean and the other with a big negative blade lean, are investigated. Both experimental measurements and numerical simulations are made for these two runners. The characteristics of efficiency and pressure fluctuations are presented, and the effects of the blade lean angles on the internal flow field are discussed. The results offer guidance to reduce the pressure fluctuations in the pump turbines while maintaining higher efficiency.
Share This Post