Pumps account for 20% of global energy consumption, and energy is often the largest cost in the life cycle costs of a pump system. Critical to a good performance pump design is the ability to systematically design high-efficiency impellers with good cavitation performance, etc.
Over the years, ADT has been involved in thousands of pump designs across all different specific speeds and applications and has developed considerable fluid dynamic knowledge to design high-performance pumps systematically; here is a summary of some of the main adverse fluid phenomena that cause a drop in performances in the impeller and pump stages.
Pump Design Process
The first step in the design of any pump is to identify the required specific speed regime of the pump. This will dictate the meridional shape and the pump's general flow direction. For example, a low specific speed pump is likely to be a radial or centrifugal type, whereas a high specific speed pump is likely to be of mixed flow or axial type.
From the required specific speed, we can identify the main flow phenomena and loss mechanisms dominant in that particular range (see figure below). For example, leakage and secondary flow effects are more dominant in lower ranges, whereas profile losses and corner separation in diffusers take priority in the higher ranges. It must be noted that a phenomenon such as cavitation can affect pumps over the entire specific speed range and must be dealt with on a case basis.
From the information above, we can use design tools and 3D CFD to investigate our pump designs; what follows are a set of principal design guidelines based on the fluid dynamics considerations of reducing dominant flow losses for a given impeller/diffuser.
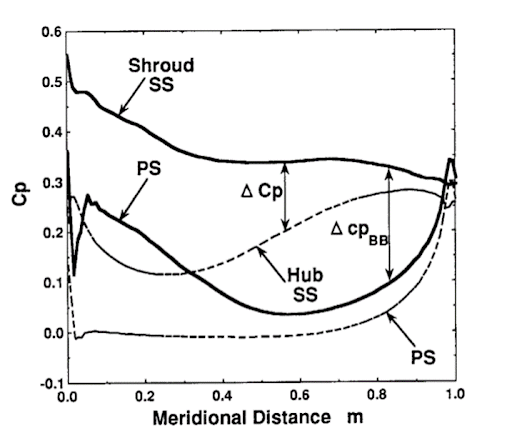
THE ISSUE
For medium-specific speed centrifugal pumps (Nq 20 to 40), the secondary flows in the centrifugal impeller are well acknowledged to drive the high-loss fluids in the viscous layer toward the shroud/suction surface corner region. The secondary flow phenomena have important detrimental effects on the efficiency and stability of the impeller. In addition, it has a dominating influence on the generation of the exit flow non-uniformity (so-called “jet-wake” flow pattern) and affects the performance and stability of the downstream diffuser.
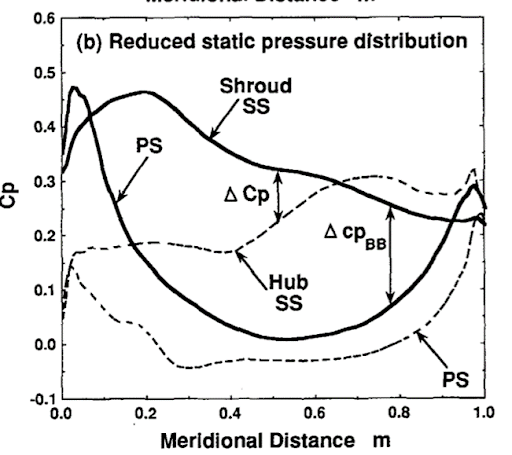
THE SOLUTION
An appropriate choice of blade loading can help reduce the pressure jump in the aft part of the blade at the shroud and increase it in the fore part, and vice versa for the hub, which helps to reduce ΔCp that is driving the secondary flow. By reducing these gradients of reduced static pressure, it is then possible to eliminate secondary flows on the suction surface, resulting in a much more uniform exit flow from the impeller.
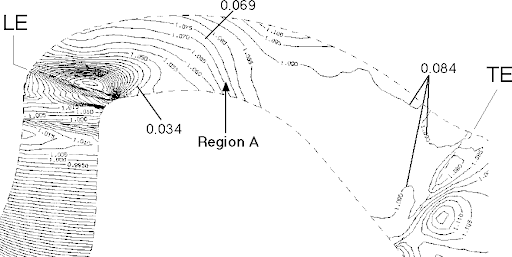
THE ISSUE
For mixed flow pumps (Nq 50 to 90), corner separation in vaned bowl diffusers happens when the low momentum fluid at the hub suction surface corner hits the strong positive pressure gradient due to the meridional geometry bend at the hub.
So, the optimization of blade shape is extremely important to avoid this large-scale flow separation along the hub suction surface corner.
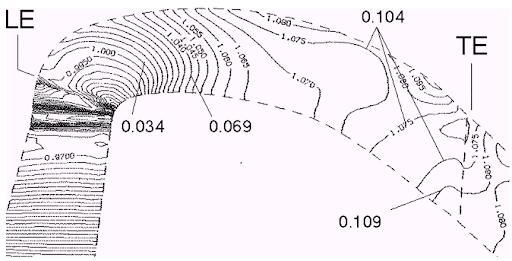
THE SOLUTION
The optimum blade loading diffuses the flow rapidly and moves the strong pressure gradient upstream near the hub. At the shroud, it results in strong secondary flows on the suction surface moving low-momentum fluids from the shroud to the hub and then to the middle of the passage. So, there is no accumulation of low momentum fluid at the endwall, and thus the corner separation can be totally suppressed.
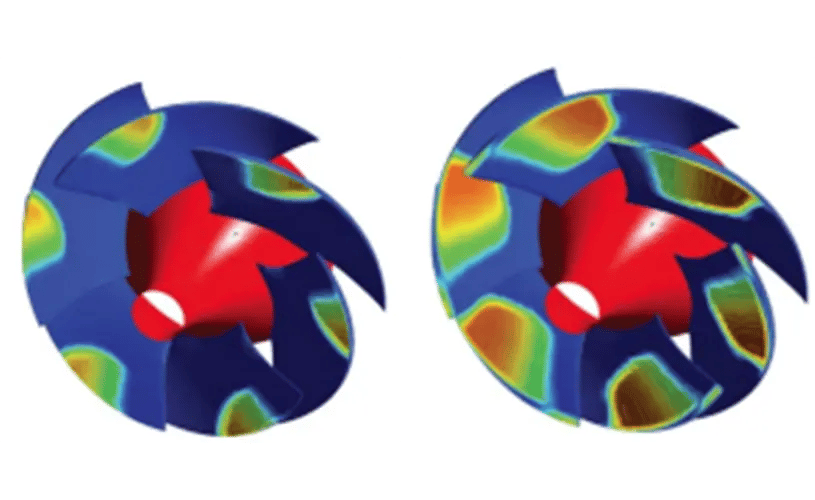
THE ISSUE
Cavitation control is a major issue in the design of pumps across all specific speeds and applications.
In many cases, it is necessary to achieve good cavitation performance while maintaining similar levels of pump performance.
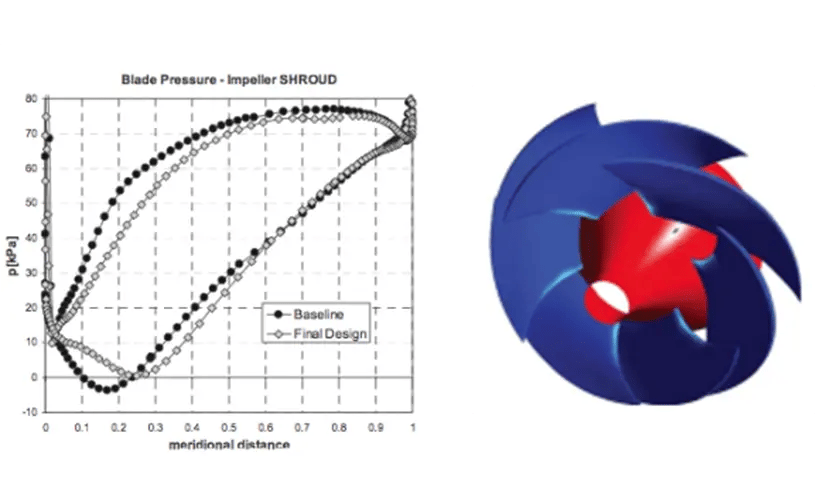
THE SOLUTION
The hub and mid-span sections, which are less critical for cavitation, can be made fore-loaded to minimize profile losses and thus maximize efficiency. However, while the shroud section is fore-loaded from 40% chord to the trailing edge, it is unloaded near the inlet to reduce the critical pressure drop in this region, mitigating the risk of cavitation inception.
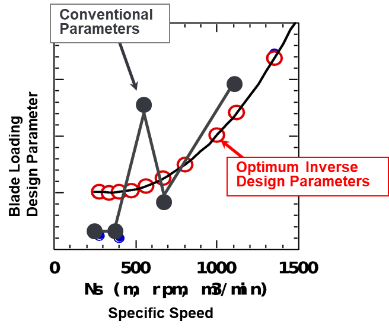
THE ISSUE
Using the above design guidelines, it is rather straightforward to develop high-performance individual pumps that, when required, provide good cavitation performance. Still, most pump manufacturers require entire series to be developed across varying flow characteristics and/or motor frequencies.
Studies made on different pump series show that traditional geometrical parameters seem to be varying quite substantially with a big scatter and there is no obvious trend line for different specific speeds.

THE SOLUTION
With design parameters based on blade loading; the information is seen to lie on a smooth curve. So, the optimized design of a pump at an intermediate specific speed is very straightforward, and a good overall performance is easily achieved. This means that there is no need to develop all the pumps in a very close specific speed range; it is possible to only develop a few and interpolate very quickly and still be able to provide customized solutions very rapidly.
Webinar on Optimum Blade Loading for Pumps
In this webinar, we demonstrate the optimum blade loading to control specific flow phenomena in pumps, such as secondary flow control in impellers, corner separation control in vaned diffusers or cavitation control in impellers.
- Learn how to use the knowledge of flow physics gained from CFD and experiments to arrive at the optimum blade loading for pumps in TURBOdesign1,
- Discover the optimum blade loading for controlling a particular flow phenomenon in pumps (e.g. secondary flow and cavitation control in impellers, corner separation in vaned diffusers),
- Understand how TURBOdesign1 provides a unique means of designing very compact pumps, which helps to reduce manufacturing costs but maintains efficiency and suction performance.
Geet Nautiyal
Geet Nautiyal is a Turbomachinery Application Engineer at Advanced Design Technology, focusing on design, marketing and customer support aspects.
View All Articles
Share This Post