Using a conventional design approach, automatic optimization is very computationally expensive as parameterizing the blade shape in 3D requires a large number of design parameters. A large number of design parameters makes use of direct evolutionary optimization prohibitively expensive, as it requires hundreds if not thousands of geometries evaluated at multiple operating points.
Furthermore, it will be difficult to ensure that the required head or Euler head is met by the geometry created at the correct flow rate and hence this has to be specified as a constraint and CFD used to evaluate the point and discard which adds to computational costs.
In order to reduce computational costs, one approach that one can use is the use of Design of Experiments approach coupled with surrogate models such as Response Surface Method or Kriging. Optimization can then be run on surrogate model to find the best trade off solution for the multiple operating points.
In this approach multi-point CFD need only be run on a small number of geometries in the design matrix. However, the key for using this approach is the accuracy of the surrogate model, i.e. to what extent the efficiency predicted by the surrogate model matches the actual values obtained from CFD of that specific geometry.
In the inverse design approach, the blade shape is parametrized by using the blade loading distribution. The code automatically ensures that all designs satisfy the specified Euler head at the correct flow rate. As a result it is possible to create accurate surrogate models by using the Design of Experiment Method.
Furthermore, a large design space can be covered by as little as 4 design parameters. Hence it is possible to use this approach for multi-point design optimization under industrial time scales. Typical optimization of an impeller at 3 operating points would only require about 45 to 60 CFD computations (i.e. a design matrix of 15 to 20 geometries computed at 3 operating points).
Download our white paper to read this content in full and discover how the advantages of 3D inverse design based multi-point optimization for pumps to improve performance efficiency by up to 4 points.
Multi-point optimization workflow
Using the inverse design method with our TURBOdesign Suite provides significant functionalities to enable designers to produce highly optimized designs faster than ever before. See the TURBOdesign workflow image.
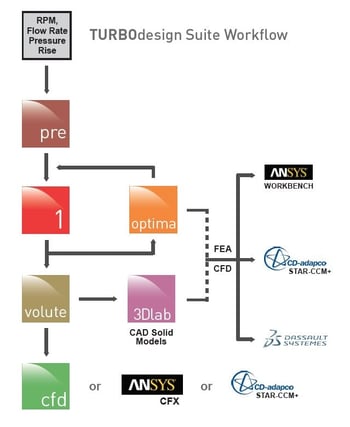
TURBOdesign Suite provides a unique platform for rapid and accurate multi-point/multi-disciplinary optimization of all types of Turbomachinery by using blade loading to “parameterize” the blade. The 3D inverse design process starts from identifying what you want to do to the fluid flow in terms of 3D pressure field, flow rate and RPM and mathematically derives the optimal geometry to achieve that outcome.
TURBOdesign1 application allows integration of TURBOdesign Optima, TURBOdesign1, TURBOdesign 3DLab and STAR-CCM+ and ANSYS workbench. The application allows the user to run an optimization case for multiple operating points that includes CFD, by means of TURBOdesign Optima. The tool allows the user to retrieve data such as efficiency, as computed, which can then be used as optimization parameters within TURBOdesign Optima.
We hosted a joint webinar with ANSYS where we show how by seamlessly integrating 3D inverse design method TURBOdesign1 into Ansys Workbench turbomachinery designers can rapidly develop breakthrough designs that meet difficult multi-objective, multi-point, multi-disciplinary requirements.
Related articles:
Share This Post