TURBOdesign Suite 2020 is coming this June. In this first look at our paradigm-shifting new software, Professor Mehrdad Zangeneh gives us an overview of what to expect and reveals the top new features.
The development and growth of the turbomachinery industry has been historically linked to petroleum products whether in power generation and related industries or in transport. However, new turbomachines can play a major role as the world tries to decarbonize. There is a need not only to develop more efficient turbomachines in existing applications but also to develop new turbomachinery used for applications such as heat pumps, Organic Rankine Cycle (ORC), CO2 capture and sequestration, energy storage and solar applications. In many of these applications the key is to design the turbomachinery not just for one operating point but multiple operating points that cover the majority of the machines’ lifecycle. Developments in new manufacturing methods such as additive manufacturing are also providing new opportunities that could be exploited by designers.

Over the past 21 years, TURBOdesign Suite and its unique 3D Inverse Design based approach to turbomachinery design has helped many leading companies in industries such as pumps, fans, chiller compressors and turbochargers to develop more efficient designs and hence has contributed in significant reductions in CO2 emissions. But given the current requirements for turbomachinery design, 3 years ago we decided to the develop, from the ground up, a new platform for turbomachinery design and create an intuitive design system that can be picked up by any engineer without much previous experience. We wanted a system that provides a simple framework to quickly come up with designs that meet the required duty point and help designers to make judgements in terms of contrasting requirements such as cavitation and efficiency for pumps, noise and efficiency for fans or efficiency and range for compressors.
This process is helped a lot by the nature of the 3D Inverse Design code TURBOdesign1, that provides not only the blade shape but also very accurate blade surface static pressure values which compares well with full RANS solutions (see Fig.1. showing a comparison between TD1 surface pressure and CFD) but at a fraction of the computational costs of CFD (taking just a few seconds on a single CPU). This accurate surface pressure and the corresponding isentropic velocity and Mach numbers can then be used to check for profile losses, diffusion on the blades and hence separations, meridional secondary flow losses and tip clearance losses. The process works not only for incompressible flow and ideal gases but for any real gas application using NIST REFPRO look up tables.

TURBOdesign Suite 2020: What's New
Fig. 2 shows a screen view of the new user interface with a typical layout. The top two plots show the current blade loading and the resulting 3D impeller shape in the form of solid IGES file. The bottom picture shows the comparison of surface static pressure and 3D blade geometry.
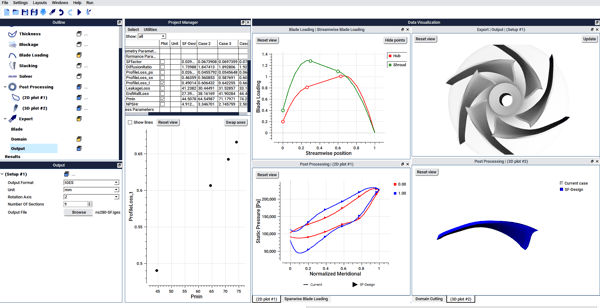
The loading is changed to that shown in Fig. 3 to reduce cavitation and immediately the comparison of the new 3D geometry and flow field versus first design case be seen in the bottom picture. Also, the resulting new impeller geometry can be seen in the top righthand figure. The project manager view can be used to monitor the design changes and to plot key performance parameters such Pmin for cavitation and profile loss for efficiency to compare different design changes.

The biggest improvements in the new TURBOdesign Suite 2020 are:
- The ability to evaluate designs in terms of changes to blade loading and then see almost instantly the effect of the changes on surface velocity and pressure as well as 2D and 3D blade geometry. This system uses the rapid computational speed of the inverse design solver and also the accuracy of its 3D flow solution
- The new project manager window enables designers to analyse their project work to arrive at new insights and know-how. Initially this uses the information derived from TURBOdesign flow field solution but in future this will also be able to extract information from major CFD and CAE systems using the automatic link between TURBOdesign Suite and major CAE systems by ANSYS and Siemens
- A flexible geometry export system that will cater for requirements for different manufacturing methods and different CFD and FEA analysis options
In the next few blogs we will explore each of these features. We have developed a number of significant improvements in new algorithms and new processes for inverse design method. These will be added to the new platform in the coming months.
Mehrdad Zangeneh
Mehrdad Zangeneh is Founder and Managing Director of Advanced Design Technology and professor of Thermofluids at University College London.
View All Articles
Share This Post